Thanks to the operation of the pulse nozzles, we provided effective separation of the material and continuous filter draining.
We solved the problem of wood dust hanging on the walls of the bag filter.
Lead time
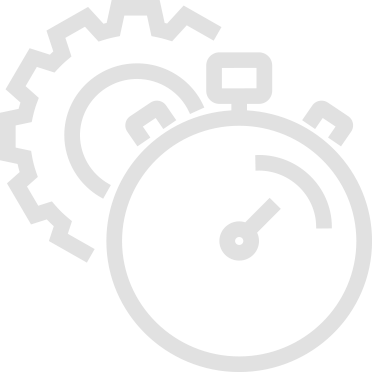
Before implementation
We delivered to the client the installation design along with assembly guidelines. The service staff made a compressed air supply with two collectors to power the nozzles. In addition, before assembling the nozzles, the client built our control cabinet with all the wires according to the Polstage guidelines. All work was done in one day while the system was operating, without the need to stop the technology.
One shift – Saturday
At that time we carried out the entire installation of pulse nozzles, along with the connection to the source of compressed air and power supply. The installation was commissioned and training was conducted for the client
Client problem
Pył drzewny zalegał na ścianach powodując nadmierne kumulowanie i zbijanie się materiału w efekcie czego podajnik ślimakowy nie był w stanie zebrać materiału do wysypu. Nagromadzony materiał powodował iż obsługa techniczna była zmuszona do ręcznego rozbijania nawisów udrażniania filtra już od włazów rewizyjnych. Każde czyszczenie wymagało odstawienia filtra i stwarzało poważne niebezpieczeństwo dla zdrowia pracowników czyszczących podajnik ręcznie.
Wood dust accumulated on the walls, causing excessive accumulation and clumping of the material, so the screw feeder was unable to collect the material for discharge. The accumulated material meant that the technical service was forced to manually break the overhangs to clear the filter from the inspection hatches. Each cleaning required the filter to be put aside and posed a serious health risk to employees cleaning the feeder manually.
Challenges
Although the material has a low bulk density and even after the overhang is quite easy to break, the challenge was to optimize the placement of nozzles and fit into the panels and filter structures. Our concept provided for the construction of two compressed air collectors so as to ensure optimal connection of the nozzle with the collector by means of a flexible hose. We prepared two separate technological collectors
An additional challenge was the assembly of the nozzle installation. The only time when a longer outage of the bag filter could occur was the weekend. That is why we wanted the installation of the nozzles and the start-up of the entire installation to take place during the planned short weekend shutdown.
- Four VA-51C pulse nozzles
- Two compressed air collectors
- Control cabinet – three algorithms of the installation’s work – which control the break time between each action of the device
- Pulse nozzles VA51C
- Fitting elements of the MPS series
- Control cabinet using Siemens LOGO PLC controller
- Reinforcement of nozzle assembly places with additional metal sheets
- Compressed air collectors adapted to plant conditions
What did we do as a part of the project?
In the design process, we performed a series of tests with materials on our test stand, which allowed us to more accurately determine the material parameters and simulate their release using pulse nozzles. These results contributed to the report provided to the client and the video of the trials, which is available on our YouTube. channel.
Using previous experience and the acquired data and analysis of the filter geometry, we designed:
- number of devices,
- optimal places for their assembly,
- control algorithms.
Apart from problem analysis, design and delivery, our task was to supervise the assembly of the installation. First, during the operation of the bag filter, compressed air collectors were made and installed, and the control cabinet was hung. Then, during the removal of the filter, employees of our client’s company made two holes in the walls and installed the nozzles together with metal sheets to reinforce them. Then the compressed air system was put into operation and tested. All the work was done during one factory shift.