We successfully eliminated the problem of coal depositing on the walls of the crusher and chutes. Thanks to the optimized work of the pulse nozzles, the devices are fully unclogged. Even poor properties coal and rainy weather do not stop production.
Lead time
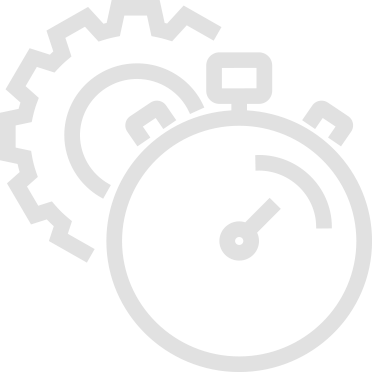
While on the move
We installed the compressed air supply system together with compressed air collectors while it was running, without the need to stop the operation of the CHP plant.
When removing the block
We were able to install the pulse nozzles and the power supply system during the planned block removing.
Client problem
Both the walls of the crusher interior and the inside and underneath chutes were covered with tape. Transported coal to the crusher had extremely poor properties that even some growths formed on the vertical walls. These finally led to blocking of the crusher and need of clean it. To do this, each time the crusher together with one of the two coal feeding lines to the boiler had to be switched off. The situation many times forced the power reduction of the block.
Challenges
The biggest challenge was to select the devices and design their arrangement in a way that would solve the problem of frequent blocking of the coal line in the section of the crushers.
The fuels used by the client had very poor transportability properties. The problems are even worse during rainy seasons. What is important, we undertook the task without setting any parameter conditions for the fuel.
An additional challenge was to coordinate the works in such a way that the installation of the nozzles and the setting up the entire installation could take place during a short maintenance shutdown.
- Installation of pulse nozzles in the crusher, on the chutes under the crusher and in the crusher inlet chutes.
- Redesign of technology elements and their assembly.
- Pulse nozzles VA51C
- Mounting elements of the MPS series
- Control cabinets based on Siemens LOGO programmable relays
What did we do as a part of the project?
We used the installation of pulse nozzles in two stages.
Stage I
Initially, due to the lack of permission for any work in the crusher (which is under warranty), we installed pulse nozzles on the chutes under the crusher and the inlet chutes to the crusher. We selected the number and arrangement of nozzles in such a way as to ensure patency both at the chutes and to partially unclog the surfaces around this zone.
Stage II
After setting up and using the nozzles for 4 months, the client commissioned us to expand the nozzle installation to include the crusher itself, putting in the first place problems with blocking the technology over the warranty. As part of additional work, we carried out a partial redesign of the acid-proof lining of the chute for the crusher and the discharge for the scraper conveyor, and then we assembled these elements.