Our next customer, in connection with the expansion of his plant, knowing the existing problems, asked for the installation of pulse nozzles on a brand new silo – a preventive measure. With a sensible approach based on the principle that prevention is better than cure, we performed a comprehensive service related to the design and installation of the pulse nozzle installation itself. Prevention is an important component of investment savings.
Lead time
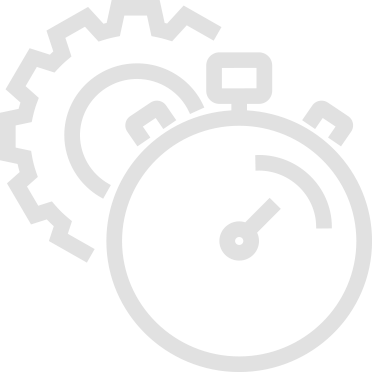
Before assembly
Thanks to the good cooperation with our client and his subordinate companies at the site, we were fully prepared with an assembly area, access to the drilling sites, scaffolding and space for the electrical cabinet.
Assembly
Making 8 holes in 8mm thick stainless steel in the confined space around the silo insulation. Installation of bolted assembly components as well as nozzle assembly including connection.
The previously prepared control cabinet was mounted on one of the silo’s structural columns. A two-part compressed air manifold was also suspended, along with a pressure gauge and pressure switch.
All of our activities could be closed temporarily within two shifts.
Customer problem
The customer’s problems with the material to be contained in the new silo are very well known from previous installation sequences. The material is very fine, oily and exhibits high hygroscopicity. The material tends to clump and hang on the walls.
In addition, in connection with the fact that the silo is seated outside, its outer surface is covered with heating mats and insulation. This makes it impossible to mechanically sharpen the silo and to add equipment without collision during the process.
Our previous testing of the material and experience allowed us to place the nozzles in optimal locations to ensure continuous transfer.
Challenges
Given that the customer’s process line would be in a state of construction and that the silo is located outside, the only time pressure was weather conditions. An additional difficulty was the silo’s insulation, specifically only small exposed sections of it allowing a small margin for manipulation with the hole saw. Other than that, the installation of the entire system went smoothly and without problems.
- A site visit, discussions with the staff as well as determining the installation locations of pulse nozzles
- Installation of pulse nozzles placed in the cone of the silo (8 nozzles VA-51C)
- Commissioning and adjustment of the nozzle algorithm to the prevailing conditions while reducing compressed air consumption
- Pulse nozzles VA-51C
- Fitting elements of the MPS-51 series
- Control cabinets based on SiemensLOGO controllers
What did we do as part of the project?
We used our experience from plastic conveying projects and performed material analysis in our laboratory.
The installation project mainly included the dedicated installation of a pulse nozzle system as well as a local control system.