Plastics, both newly produced and recycled, are undoubtedly a highly expansive group of materials we deal with in plants. Also in this case, waste material from the production of PVC board elements in the form of chips was the subject of the action. Containers with large amounts of PVC shavings undoubtedly tend to get stuck on their own, as our client experienced. Fortunately, a small dose of compressed air applied in an appropriate manner allowed for full patency.
Lead time
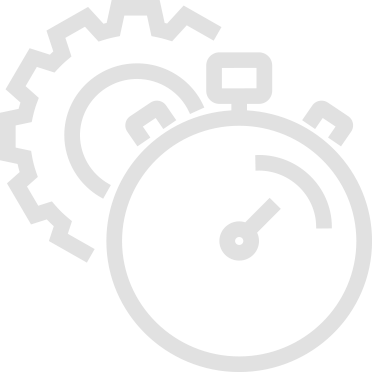
Assembling the installation consisted of making holes and installing mounting elements in them, then nozzles, and assembling the control cabinet with cabling. The collectors and compressed air connections were made by the company’s services. The seemingly small installation performed during shutdown had a longer implementation time due to the severely limited working space around the chute and feeder. Additionally, winter conditions during the outdoor installation did not help operations. However, despite the difficulties, our efficient and well-coordinated team was able to complete everything in one day.
Client problem
Blocking of material in the form of PVC chips in the change of the geometry of the transfer and in the silo hopper. The problem is aggravated by the use of vibrators, which further compact the material. The bottom of the cone ended with a head with a hole instead of a cone narrowing to the diameter of the pipe, causing additional difficulties.
The screw receiving material from the cone and transferring it for further transport had a feed and discharge of material as critical places. Blocking due to material adhering to the walls resulted in frequent shutdowns of the transport line and the need to clean it.
Challenges
Extremely small amount of space for installing nozzles on higher levels due to the structure of the entire silo. A cylindrical cover with the diameter of the silo meant that the place where the geometry changed from a cylinder to a cone created a small space for installing nozzles. Therefore, it was necessary to lower the top level to a level where the nozzles could be installed.
Additional challenges included:
- working in a dusty, flammable environment
- making holes in a small space and on small diameter elements – screw feeder
- Selection of assembly elements to the assembly possibilities at the facility;
- Installation of pulsation nozzles placed on the conical chute and in the screw feeder;
- Launching and adapting the nozzle operation algorithm to the prevailing conditions while limiting compressed air consumption;
- VA51SS pulsation nozzles – 4 pcs.
- VA06SS pulsation nozzles – 2 pcs.
- Special MPS screwed and MPN welded mounting elements
- Flexible hoses
- Control cabinets based on Siemens LOGO programmable relays
What did we do as part of the project?
As part of the project, as in the vast majority of cases, we visited the plant to inspect the site and identify problems on site. Talking to support and seeing the problem with your own eyes is the best tool to start solving these problems.
After the vision, we also received a sample of the material we were to work with, which made it possible to test the material in our laboratory. Even more detailed knowledge of the properties, discharge angle and the best imaging of tests in a test tank. Testing the effectiveness of nozzle placement on a scale is the fastest way to design an installation dedicated to current needs and to learn for future activities with this material.
Armed with knowledge and a complete picture of the problem, we designed the installation along with the arrangement of nozzles on the silo and the screw feeder.
The next part was coordinating the works on the construction of pipelines, collectors and the implementation of the instrumentation and control system connecting our control cabinets with the control system of the heat and power plant.
Coordination of work, resulting in punctuality and full effectiveness of operation, ensured that the installation started operating as quickly as possible. After installation, our specialists controlled the work to quickly and effectively develop installation operation algorithms. It was extremely important to control the operating time of devices and their frequency. Finally, programs were selected that are effective to this day.