Corrosion of metals is undoubtedly an undesirable phenomenon, but water is not the only thing that can have a bad effect on metal. It also interacts unfavorably with the rubber components of impulse valves. Therefore, it is extremely important to both prevent the entry of condensed water from the compressed air, but also to prevent the system from accumulating water. The solution to preventive measures is automatic condensate discharge.
Lead time
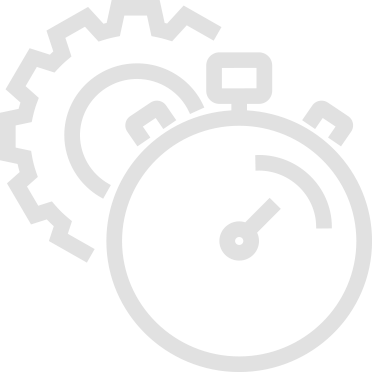
Before installation
In preparation for operation, the repetitive systems of drainage components, sensor and valve connections were refabricated into a new system including liquid level sensors and a solenoid valve. Repetitive control circuits were also prepared so that all that needed to be done on site was to plug in the signal wires.
Installation
Installation of the drainage system took place in two stages. The first stage took place during the service inspection of the nozzles, at which time the electrical wires were distributed and the drainage systems for the manifolds were installed. The second stage was the installation of controls and electrical connection of the system. The whole operation can be estimated at less than one shift.
Customer problem
A common problem of small air compression systems is incomplete separation of condensed water. Since a separate compressor with its own buffer is used for the installation of pulse jets installed on coal bunkers, rather than a plant air preparation system, this dehydration problem was quite troublesome. The constant appearance of water in the system not only causes corrosion of the manifolds, but also adversely affects the pulse valves, especially the valve diaphragms. This is the reason for the need for frequent service and replacement of worn components.
- Liquid level measurement
- Time relays
- Drainage valve controlled according to liquid level as well as periodically preventively by time relays
- Starting and adjusting the time of checking and opening of valves.
- Liquid level sensors with controller
- Timing relays to allow and control the opening status of the valves
- ASCO impulse valves
What did we do as part of the project?
Prefabrication of individual drainage systems including liquid level sensors and solenoid valves.
Two-stage dewatering control – depending on the liquid level as well as time-preventive control
Routing of control cables and signaling of system operation on existing control cabinets.