The installation of an oil sampling station, which allows for sampling from the pipeline transporting oil to the biomass-fired boiler, enabled the implementation of modern fuel quality monitoring solutions.
The new control system enabled the ongoing analysis of oil parameters, which is crucial for maintaining stable and efficient combustion conditions in the boiler.
The introduction of an automated sampling system increased the reliability of the technological process and enabled the rapid detection of any contaminants or quality deviations that could negatively impact the system’s efficiency and the environment.
Systematic oil quality monitoring contributes to the optimization of the combustion process, reducing emissions of harmful substances into the atmosphere, such as CO₂, SO₂, and NOₓ, and supporting environmental protection efforts.
This installation is an important element of the plant’s strategy to increase energy efficiency, improving boiler operational reliability and aligning with the goals of sustainable development and responsible management of biofuels.
Lead time
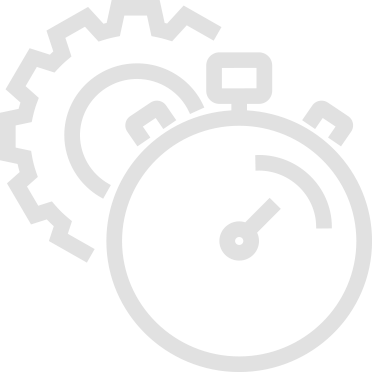
The installation of the sampler was preceded by a site visit, during which the designer determined the technical requirements and the optimal installation location.
Based on these findings, a technical design was developed, tailored to the specifics of the existing installation and operating conditions.
The next step was to assemble the mechanical components and automation system for the sampler, enabling automatic and repeatable oil sampling without the need for operator intervention.
The installation will be carried out with integration into the existing pipeline infrastructure, allowing for efficient system implementation and the commencement of ongoing quality monitoring of the medium transported to the biomass-fired boiler.
Customer problem
The current lack of an automatic oil sampling system resulted in numerous operational limitations and the risk of measurement errors. Manual sampling was time-consuming, fraught with the risk of inconclusive results, and required shutting down or limiting the system’s operation, which negatively impacted the continuity of the combustion process.
The lack of continuous monitoring of oil parameters hindered ongoing assessment of the quality of the fuel fed to the boiler, which could lead to poor combustion conditions, increased system wear, and increased emissions of harmful substances.
Challenges
The sampler system was designed for automatic and cyclical sampling of EKOTERM PLUS or BIODIESEL RME (B, D, F) heating oil from the pipeline feeding the biomass-fired boiler at the Szczecin Power Plant.
It is a key element of the fuel quality control system, providing representative samples without requiring operator intervention in the ongoing operation of the system.
The system consists of a sampling system (sampler), pipelines connecting it to the existing oil system, and a control and monitoring system for the device’s operation.
The sampler is designed to work with a DN50 pipeline with strictly defined operating conditions:
- working pressure in the range from 0.8 MPa to 1.2 MPa,
- medium temperature from +5°C to +25°C.
The use of this installation allows for obtaining reliable data on the quality of the fuel entering the boiler, which has a direct impact on the efficiency of the combustion process, occupational safety and compliance with environmental requirements.
- The sampling system (sampler) is a key element of the installation, responsible for the cyclical, automatic collection of heating oil samples in a safe and repeatable manner.
- Connecting pipelines connect the sampler to the boiler’s main oil system. Designed to meet the pressure and temperature requirements of the medium.
- The control and monitoring system is responsible for automating the device’s operation and monitoring its technical condition.
- DN10 flanges PN1.6 MPa for connecting oil pipelines,
- DN10 manual valves (Z74, Z75) with limit switches,
- DN10 electric valves (Z71, Z72, Z73) with actuators and limit switches,
- sample tank with 4-20 mA pressure sensor,
- receiver tank with optical and analog level gauge,
- carbon filter for vapor reduction,
- Z76 valve for manual sample collection with limit switches,
- Z77 receiver tank with drain valve,
- heating system with thermostat (71EGD30AH001) maintaining 25°C,
- thermal insulation (~50 mm), *support frame,
- control cabinet (71EGD10CX001) with indicator lights and buttons.
- The sampler is designed as a standalone, electrically controlled device mounted on a support frame and delivered as a complete, assembled unit, ready for connection to the oil system.
- Automatic collection of individual oil samples (up to 50 ml) at specified intervals and collection in a tank with a capacity of approximately 2.5 liters to obtain a daily sample for laboratory testing.
- The sampler is located outside explosion or fire hazard zones, inside the boiler room.
- Sampling of uncontaminated Ekoterm Plus heating oil or bioester, in accordance with the requirements of DIN 51603-1 and PN-EN 14213, with a maximum particle size of up to 0.2 mm.
- Connection of the device to a DN50 pipeline with an operating pressure of up to 1.2 MPa and an operating temperature range of +5°C to +25°C.
- Use of a control system with local an operator console enabling the display of messages about the sampler’s operating status and the change of sampling frequency.