Small installations handling seemingly loose and fine materials can cause significant problems. The plastic material used on the surface, EPS, or expanded polystyrene in the form of particles, is a slippery material, but the content of a wide range of fractions creates ideal conditions for adhesion in sensitive areas of the installation. Thanks to the well-known installation of nozzles by our customer, he decided to use a very small installation, but completely sufficient and effective, replacing the combination of vibrating bottom with conventional hammer blowing.
Lead time
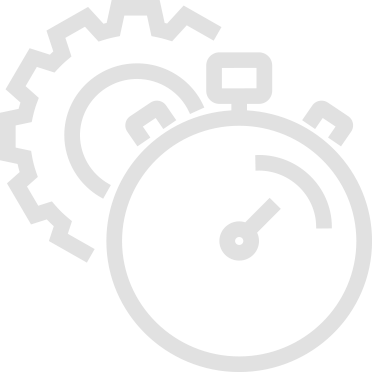
Before Assembly
Our task was not only to design and install the pulse nozzle, but also to make a new cone for the silo that holds the material. The new cone is devoid of any mechanical damage caused by hammering, vibrating bottoms and the chute angle is improved.
Prefabrication of the cone also included workshop preparation of welded mounting elements for two pulse nozzles.
Prior to installation, the compressed air manifold, the control cabinet, and the compressed air supply of the electrical system supplying the control cabinet were also installed at the site.
Assembly
Due to the fact that the installation as part of the process line is an important point, and there was no putting off the entire line, we had to perform all the activities in one shift. We carried out the activity to remove the existing cone, install the new one and install the pulse nozzles in 5h.
The prior preparations and the efficient operations of the teams at the plant made the work proceed in an exemplary and trouble-free manner. In less than one shift, the installation of the pulse nozzles was put into operation, along with operator training.
The client problem
The bottleneck of the discharge was both the cell feeder, the plastic compensator, which, moreover, is part of the transition of the discharge geometry from circle to rectangle. An additional impediment to emptying the cone was the too-smooth angle of the side surface.
Challenges
Given that the customer’s process line would be in a state of construction and that the silo is located outside, the only time pressure was weather conditions. An additional difficulty was the silo’s insulation, specifically only small exposed portions of it allowing a small margin for manipulation with the hole saw. Other than that, the installation of the entire system went smoothly and without problems.
- Site inspection, material testing, design of new cone part including its replacement
- Installation of pulse nozzles placed on the silo cone (2 VA-06SS nozzles)
- Commissioning and adjustment of the nozzle algorithm to the prevailing conditions while reducing compressed air consumption
- Pulse nozzles VA-06SS
- Fitting elements of the MPN-06 series – welded mounting elements
- Control cabinets based on SiemensLOGO controllers
What did we do as a part of the project?
Using our experience in design and knowledge of bulk material flow, we selected an optimal solution to improve the flow with little interference in the existing equipment.
By testing the material in our laboratory, we additionally learned about the properties of the material and more precisely selected the individual components of the plant to improve production.