Due to the installation of pulse nozzles on coal chutes, we eliminated the problem of repeated blockage. The preventive and optimized operation of the nozzles ensures the patency of the chutes, therefore- the continuity of pouring coal into the boiler. Even low-quality coal with very high humidity no longer stick on the walls of the chutes.
Lead time
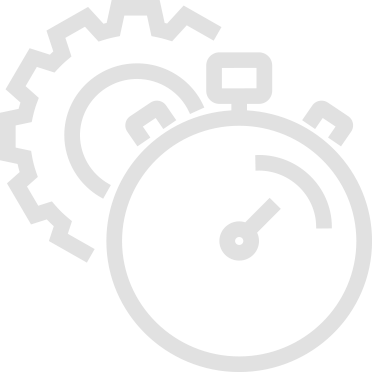
Before start
We designed the assembly elements in such a way as to best fit the curvature of the pipe chutes and to increase the effectiveness of the nozzles. We integrated specially designed assembly elements into new fragments of the chute, which we installed in a way that facilitates assembly work.
During temporary shutdown of the power unit
Previously prepared fragments of chutes with welded assembly elements were installed during the planned block removal related to the annual service. At that time, we also expanded the compressed air infrastructure with collectors.
Apart from that, we created an electrical installation, which supposed to power and control the nozzles. Then we installed the pulse nozzles along with the power devices.
Client problem
The fragments of the chute pipelines under consideration are both in the vicinity of compensators and in the place where the geometry of the pipeline changes. Once poor quality coal and high humidity combined together it caused coal deposition on the walls of the chute, layer by layer. This process was rapidly growing. Consecutive layers resulted in faster and faster overgrowing of the canal cross-section. This process led to a reduction in the amount of fed coal, same time to decrease the power and efficiency of the power boiler. Despite the use of de-scaling agents by the staff, mechanical cleaning and scraping of the coal was the final solution. This could only be done during withdrawal, which generated significant losses.
Challenges
At the beginning of the project, it was quite a challenge to install the nozzles in such a way as to achieve the highest possible efficiency by flattening the chute surface, but without having to reduce its cross-section.
Additional challenges:
- efficient coordination of works between subcontractors,
- maintaining the highest quality of activities,
- full supervision over the execution.
Every stage of this project had to be of the highest quality due to the precise fit of all elements.
- Designing special mounting elements adapted to the diameter of the coal chutes used;
- Installation of pulse nozzles placed on 4 chutes in the most critical places (4 chutes with 6 nozzles each);
- Launching and adapting the nozzle operation algorithm to the prevailing conditions while reducing compressed air consumption
- Pulse nozzles VA51C
- Special mounting elements of the MPN series, extended with a properly shaped work surface
- Control cabinets based on Siemens LOGO programmable relays
What did we do as a part of the project?
We used our experience from previous projects related to the transport of coal and conducted an in-depth analysis of the fuel feeding process and the geometry of the carburizing system. We designed installations of pulse nozzles in four independently powered and controlled zones of the carburizing system.
The design of the installation mainly included a dedicated installation of a system of pulse nozzles. It was also a very important task to provide a system control solution that would be most compatible with the entire control system of the CHP plant, I&C. Because of this, we were able to synchronize the work of the nozzles with the tasks of other devices built into the carburizing system. Effect? Highest efficiency and high level of automation.