The installation of pulsating nozzles has eliminated the recurring problem of coal chute obstruction. Preventive cleaning of sensitive areas on the wall has ensured the continuity of the chute and the absence of the need for service interference as part of mechanical cleaning. Continuity of the chute is maintained and thus ensuring efficient boiler operation.
Lead time
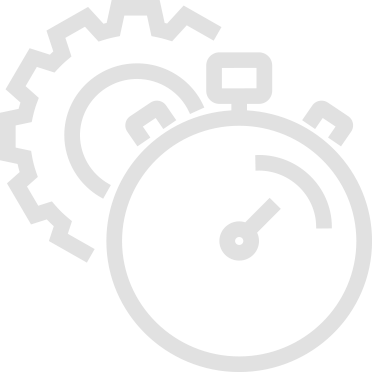
Before installation
Before the installation of the pulsating nozzles, compressed air manifolds were designed, fabricated as well as installed. The assembly, fabrication as well as connection of the manifolds rested with the plant companies with our supervision.
Control cabinets were also prepared in advance, as well as the completion of equipment components included in the pulsating nozzle installation for the particular assembly solution.
During the coal feed threading off
Making 8 holes in the double walls with difficult access to the center of the chutes as well as limited space around the working area. Installation of mounting elements with wear-resistant sheet metal as well as nozzle installation including connection.
Pre-prepared control cabinets were installed at the nozzle work area, and control cables were distributed after the installation of the pulsating nozzles.
Customer problem
Due to the deteriorating quality of the fuel, the geometry of the coal chutes for the screw feeder was a contributor to wall cladding. The buildup of solid fuel over time resulted in a restriction of the fed material thus to a decrease in the power and efficiency of the power boiler as well as problems with removing the backed-up material.
Despite lining the chutes with stainless steel or plastic, the sticking effect continued. The final solution was mechanical cleaning and scraping of the coal. This, in turn, could only be done during haul-off, which generated significant losses.
Challenges
One of the biggest challenges in this sentence was the limited operating time. Both the time to prepare for the installation and the time to install it. Efficient logistics and execution activities, as well as stockpiles, allowed the time from order to execution to be reduced to a minimum. In addition, the installation of coal feeding after all also put off due to other repairs is the time that was allocated for the installation of nozzles was no more than 48h. The density of the installation’s other equipment, the limited time as well as the drilling of double walls posed a challenge, but not one that could not be met. Our installers also efficiently dealt with newly arising problems during the work.
- Site inspection, discussions with the staff as well as determination of the locations of installation of pulsating nozzles
- Installation of pulsating nozzles placed on 2 chutes in the most critical areas (2 chutes on each 4 nozzles)
- Activation and adjustment of the nozzle algorithm to the prevailing conditions while reducing compressed air consumption
- Pulse nozzles VA-51C
- Fitting elements of the MPS-51C-TK2 series – elements with wear-resistant steel plate
- Control cabinet using Siemens LOGO PLC controller
What did we do as part of the project?
We used our experience from coal handling projects and conducted an in-depth analysis of the fuel feeding process and geometry of the carburization system. We designed the installation of pulsating nozzles with local control.
The installation design mainly included dedicated installation of the pulsating nozzle system as well as the local control system.