To maintain production at the highest level, not only in terms of quality but also in terms of volume, one of Poland’s leading chemical companies needed to effectively support the flow of ammonium sulfate. This material is extremely hygroscopic and significantly affects metal corrosion. Difficult to transport, it requires a leak-free and efficient installation. Employee safety in this industry is all the more crucial, making a maintenance-free unclogging system key to efficiency.
Schedule of activities
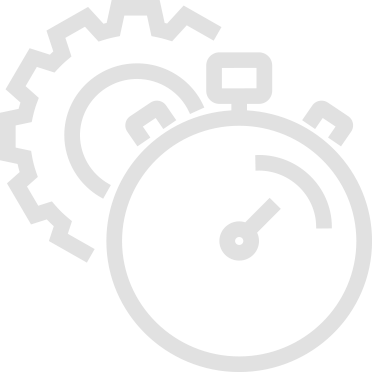
Preparation stage (before assembly)
In the first phase of implementation, we conducted conceptual work, selected technology, and negotiated detailed agreements with the client.
This stage included:
- analysis of ammonium sulfate discharge problems and assessment of the tanks’ technical conditions,
- design of the pulse nozzle system and the location of assembly points,
- selection of components resistant to aggressive environments,
- coordination of activities with the maintenance and plant automation departments,
- determining the date and scope of assembly work during the line shutdown.
Assembly and commissioning stage
After the design was approved, we began installing the pulse jets and integrating them with the plant’s control system.
This stage included:
-
drilling and installation of nozzles in the stainless steel tank walls, installation of pneumatic and compressed air systems,
-
connection of the control system to the existing automation system,
-
commissioning tests, parameter calibration, and operational tests,
-
staff training and documentation delivery.
Customer problem
Before installing the pulse nozzle system, the client was struggling with serious operational problems related to the transfer and storage of ammonium sulfate in the tanks. Due to its physicochemical properties (hygroscopicity, tendency to caking, and electrostatic adhesion to surfaces), this product caused significant disruptions in the material’s flow process.
Over time, the following occurred in the tanks:
- product accumulation on the silos’ walls, where ammonium sulfate adhered and settled in hard, difficult-to-remove layers;
- material bridging, i.e., the formation of product arcs above the hopper outlet, which blocked the free downward flow of sulfate;
- the formation of empty tunnels through which the material only slid centrally, leaving significant amounts of product adhering to the walls and unused in the production cycle.
These phenomena resulted in frequent production downtime, the need for manual intervention (e.g., mechanically clearing blockages), and an increased risk of equipment damage or health and safety hazards for personnel. The problem was recurring and became particularly severe during periods of high humidity.
The client attempted to resolve the situation using traditional vibration isolation and manual unblocking methods, but these proved insufficient and ad hoc..
Challenges
The installation of pulse nozzles on ammonium sulphate tanks was associated with a number of significant technical, organisational and environmental challenges that required precise planning and appropriate preparation of the assembly team.
- Aggressive work environment – high corrosivity
Ammonium sulfate exhibits highly corrosive properties, especially in the presence of moisture, necessitating the selection of appropriate assembly materials and extreme caution when working in direct contact with the product. This required the use of chemically resistant components (e.g., seals and fittings made of stainless steel or special plastics). - Intense, irritating sulfate odor in the air
During assembly work, especially in confined spaces near the tanks, high concentrations of irritating ammonium sulfate vapors persisted, negatively impacting work comfort and safety. Appropriate personal protective equipment (masks with filter cartridges, workplace ventilation) and limiting employee exposure time were necessary. - Drilling holes in stainless steel tanks
Installation of the nozzles required precise drilling in the stainless steel tank walls. This operation carried a significant risk of structural damage to the tank and required the use of specialized tools and drilling techniques, taking into account the thickness and resistance of the material. Working at height and in a confined space was an additional challenge. - Production Line Shutdown
Due to the nature of the work and the risk of product contamination during interventions in the tank structure, the production line had to be completely shut down for the duration of the installation. This required close collaboration with the maintenance and production teams to minimize downtime and avoid disruptions to the production schedule. The work had to be completed within a short, pre-planned maintenance window.
- Installation of pulse nozzles in ammonium sulfate tanks to eliminate bridging, material adhesion to walls, and the creation of discharge channels.
- Nozzle selection and placement based on analysis of tank geometry and product properties.
- Construction of a pneumatic system to supply the nozzles with compressed air.
- Integration with the plant’s control system, enabling automatic and manual control of nozzle operation via HMI or PLC.
- Assembly work in demanding conditions, including drilling in stainless steel and installation in chemically aggressive environments.
- Commissioning, functional testing, and optimization of nozzle settings for cleaning efficiency.
- Staff training and provision of technical documentation.
- Pulse nozzle VA51-SS
- Pulse nozzle VA12-SS
- Pulse nozzle VA06-SS
- Welded mounting elements
What did we do as part of the project?
As part of the ammonium sulfate storage tank modernization project, our team comprehensively installed a pulse nozzle system to eliminate problems related to bridging, material buildup on walls, and the formation of discharge tunnels. The scope of work included:
- Design and selection of an appropriate pulse nozzle system
Based on the analysis of the tank parameters and the properties of ammonium sulfate, an optimal system of compressed air nozzles using pulse technology was selected, adapted to the tank geometry and the plant operating conditions. - Installation of pulse nozzles
The nozzles were drilled and installed in the stainless steel tank walls, maintaining full tightness and corrosion resistance. High-quality components resistant to the aggressive ammonium sulfate environment were used. - Construction of a pneumatic installation with air supply distribution
The compressed air supply is routed to each nozzle, with appropriate distribution, valves and safeguards to ensure uniform and efficient operation of the system. - Integration with the plant control system
The nozzle control system was integrated into the existing plant automation system, enabling full control over blow-off cycles directly from the operator. An interface was created allowing for the configuration of operating parameters (time, sequences, frequency), with the option of automating operation based on signals from the process line. - Start-up tests and optimization of operating parameters
After installation, system start-up, functional tests, and calibration of the pulsation settings were performed, adjusting the intensity and frequency of the purge to the physical properties of the ammonium sulfate and operating conditions. - Staff training and submission of as-built documentation
The plant’s technical team was trained in system operation and maintenance. The client received full technical documentation and an operating manual for the system.