The goal of the project was to improve the flow and discharge of dolomite stored in large concrete silos, where material flow irregularities and blockages were disrupting operations. To solve these issues, a pulse jet cleaning system was installed, consisting of three pulse jet nozzles and a compressed air manifold.
Project Timeline
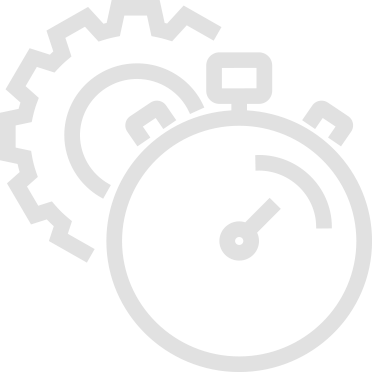
Pre-installation Phase
During the initial phase, we carried out:
-
A site visit and analysis of the silo flow behavior and dolomite properties,
-
Selection and layout design of the pulse nozzles for optimal placement,
-
Design of the pneumatic air supply system (including manifold and piping),
-
Coordination with the client’s technical and maintenance teams to align on installation points, access, and system integration,
-
Preparation of work plans for execution during a scheduled plant shutdown.
Installation and Commissioning Phase
The second phase included all on-site installation and system commissioning:
-
Core drilling into thick concrete silo walls, using specialized diamond drilling tools to ensure precision and structural safety,
-
Installation of 3 pulse jet nozzles at the designated locations,
-
Assembly and mounting of the compressed air manifold and distribution piping to each nozzle,
-
Air leak testing and system pressure checks,
-
System start-up and calibration of pulse parameters (pulse duration, interval),
-
Operator and maintenance team training,
-
Handover of as-built documentation and commissioning reports.
Client’s Problems
Before the installation, the client was experiencing typical flow issues associated with bulk materials like dolomite:
-
Material buildup along silo walls,
-
Bridging and arching above the discharge outlet,
-
Irregular flow and funneling, leading to the formation of empty “chimneys” through the product,
-
Frequent need for manual intervention, causing production downtime and safety risks for the maintenance team.
These issues negatively impacted production continuity and increased maintenance costs.
Installation Challenges
Several technical challenges were encountered during this project:
-
Drilling into thick concrete walls, requiring precise execution and reinforcement of mounting points,
-
Limited access around the silos and work at height, requiring special safety measures,
-
Integration with the existing compressed air infrastructure,
-
Strict time constraints due to the need to complete work within a predefined maintenance window.
-
We implemented high-efficiency pulse jet nozzles, resistant to dust and wear from abrasive materials like dolomite,
-
A custom-designed compressed air manifold was fabricated and installed,
-
Nozzles were strategically positioned to ensure complete coverage of the cone area and eliminate flow disruptions,
-
The system can operate in automatic or manual mode, controlled by plant personnel, improving safety and reducing manual silo clearing.
- Pulse nozzle VA51-C
- Special, screw-on mounting elements
What We Delivered as Part of the Project?
-
Analysis of operational issues and technical evaluation
We carried out on-site assessments to identify where flow obstructions occurred and to understand the material’s behavior in the silos. -
Design of a complete technical solution
We designed the nozzle layout, selected suitable components, and planned air distribution based on silo geometry and material characteristics. -
Supply of all system components
This included the pulse jet nozzles, air manifold, fittings, pneumatic lines, valves, and mounting hardware. -
Concrete drilling and nozzle installation
Precision core drilling was performed to install the nozzles securely into the concrete silos without compromising structural integrity. -
Compressed air system installation
Air lines and the manifold were installed and connected to the plant’s existing compressed air supply system. -
System start-up and tuning
The system was tested, tuned, and adjusted to optimize performance for dolomite discharge, minimizing pulse frequency and air consumption. -
Operator training
Maintenance personnel were trained on system operation, maintenance schedules, and safety procedures. -
As-built documentation and system handover
We delivered full technical documentation, operating manuals, and startup reports. The system was handed over as fully operational.