The installation of pulse nozzles has relieved the CHP plant operator of unnecessary hammer interference while increasing the reliability of the carburisation system. Coal chute scouring is a common problem. The use of increasingly poorer quality fuel does not help to reduce this phenomenon. By installing pulse jets on the coal chutes, we have eliminated this problem. The preventive operation of the installation effectively treats the build-up of coal on the walls.
Lead time
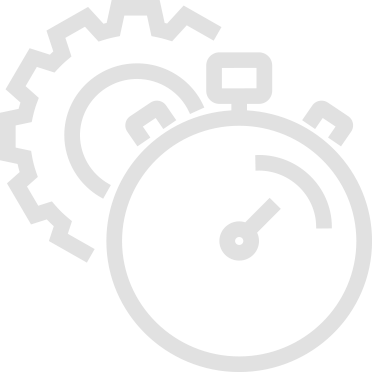
During temporary shutdown of the power unit
The installation was carried out in two stages and with the cooperation of plant companies. The pulse nozzles are installed in the inspection flap of the coal chute. As a result, the preparatory and assembly work could be carried out partly in the workshop, which undoubtedly has a positive effect on speeding up the work and reducing costs.
Holes were drilled in the prepared chute flap and mounting parts were welded in place. The flaps were then ready for installation on the site.
At the same time, the factory companies carried out the compressed air installation including manifolds, as well as the electrical and control connections, linking our control cabinets to the factory’s control and instrumentation.
Client problem
A common place where material transfer problems occur is any change in geometry. There is, and similarly in this case, an area of change in the angle of the chute pipe. Combined with the high moisture content of the coal, this was a place where coal clung and built up in one place making it difficult to transfer. This process led to a reduction in the amount of coal fed and thus a decrease in the power and efficiency of the power boiler. Despite the use of build-up removers by the operator, the ultimate solution was to mechanically clean and scrape the coal. This, on the other hand, could only be done during the shutdown, which generated significant losses.
Challenges
Limited space around the chute pipes. The multitude of fixtures and the proximity of other structures made it difficult to reach the chute pipes and place our installation there.
Additional challenges included:
- efficient coordination of work between subcontractors,
- maintaining the highest quality of operations,
- full contractor supervision.
Work at every stage of the project had to be of the highest quality due to the precise fit of all components.
- Prefabrication of pulse nozzle assembly components in chute flaps;
- Installation of pulse nozzles placed on 4 chutes in the most critical areas (4 chutes with 3 nozzles on each);
- Activation and adaptation of the pulse nozzle algorithm to the prevailing conditions while reducing compressed air consumption
- Pulse nozzles VA51C
- Special mounting elements using MPN series components
- Control cabinets based on Siemens Simatic programmable relays
What did we do as a part of the project?
We designed the installation including the positioning of the nozzles on the existing coal feed line and prepared the installation locations for the pulse nozzles themselves.
The next part was to coordinate the works of piping, manifolds and the execution of the control and instrumentation installation connecting our control cabinets with the control system of the CHP plant. The coordination of the work topped off with punctuality and complete efficiency ensured that we were able to get the plant up and running as quickly as possible. After installation, our specialists monitored the work to quickly and effectively fine-tune the plant’s operating algorithms in conjunction with the DCS control system. It was extremely important to control the operating times of the equipment and their frequency. Ultimately, programmes were selected which are still running effectively today.