We provided patency in a weighing tank with a mixer that handles 3 different materials (potassium sulfate, regypsum and turkey manure). Three algorithms of operation of pulse nozzles guarantee constant pouring of materials in the tank.
Lead time
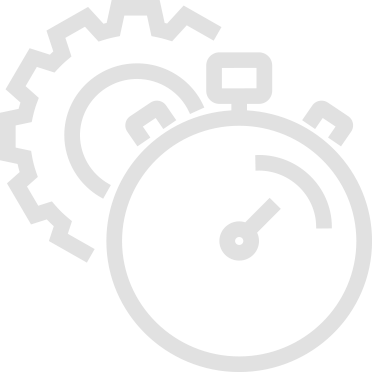
2 days
That’s how long it took us to install the pulse nozzle installation. And we did it simultaneously with two additional works on other technologies.
A few weeks
That was a time of ordering process and the time to complete the project. Close cooperation of our designers with specialists on the client’s side allowed us to prepare a technology model (the client did not have such detailed documentation). Thanks to this, we were able to conduct an online arrangements without the need to take additional measurements before installation.
Client problem
A weighing tank with a mixer works on a fertilizer production line. There are transported, weighed and fed, several materials with very different properties. This situation caused jamming issues and required staff intervention each time. The materials used are: potassium sulphate from biodiesel production, plasterboard and turkey manure. The properties of the materials caused problems with the smoothness of feeding and dropping out from the tank as a result of overhangs that disturbed the operation of the strain gauges.
Challenges
The main challenge was to design an installation that would effectively solve different types of problems generated by different materials.
Potassium sulphate and regypsum are loose materials of high density, viscosity and tendency to block narrowing discharges. On the other hand, turkey manure is a lighter material with a heterogeneous fraction with fibers that, when tangled, can very effectively clog the tank outlet.
- Installation based on 2 VA51SS pulsating nozzles and 2 VA06SS pulse nozzles built on 2 levels for full unblocking of the discharge part and cleaning the surface of vertical walls.
- Programming of 3 different nozzle operation algorithms (gentle, optimal and aggressive) – the choice of option is made by maintenance stuff depending on the current parameters of the materials
- Pulse nozzles VA-06SS
- VA-51SS Pulse Nozzles
- mounting elements of the MPN series
- Control cabinets based on Siemens LOGO programmable relays
What did we do as a part of the project?
In the design process, we performed a series of tests with materials on our test stand, which allowed us to more accurately determine the parameters of materials and simulate their release using pulse nozzles.
Using previous experience and the obtained data and analysis of the geometry of the tank, we designed the number of devices, optimal places for their assembly and control algorithms. Devices and assembly accessories that are exposed to constant contact with corrosive materials are made of acid-resistant steel.