This is one of our fastest, but also the most comprehensive implementations. Thanks to the installation of pulse nozzles, we eliminated the phenomenon of coal suspension in the carburizing system of the CFB fluidized bed boiler.
Lead time
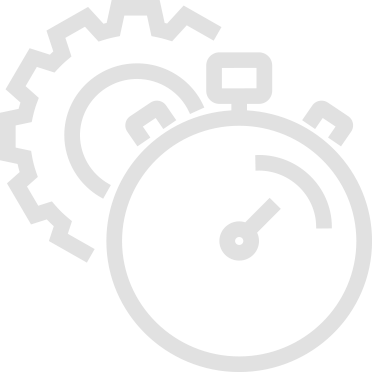
Before start work
Thanks to the previous cooperation with Polstage, the technical services were perfectly familiar with the details of the operation of the pulse nozzles. Very good communication and a clearly defined goal allowed us to quickly adjust the parameters of the system and fully implement the project assumptions.
3 months
That’s how long it took us for one of our fastest and most comprehensive projects. In just over 3 months we completed the following tasks:
- technical arrangements
- obtaining an order
- implementation of multi-discipline projects
- delivery of equipment, prefabrication and replacement of some steel elements
- mechanical and electrical assembly
- start-up, optimization and staff training
Client problem
The installation for feeding coal to the fluidized bed boiler was clogged on many sections and required constant, mechanical intervention of the power plant services. In some zones (which we refer to as bottlenecks due to their shape and geometry), hammering or plant shutdowns and scraping were very frequent. After each delivery of wet fuel or during rainy periods when the coal became very viscous and clayey there was need of clearing.
In addition to the very high workload of the power plant employees, a pressing problem was the underestimated power of the block and the need for emergency feeding of kindling oil, which entailed high costs.
Challenges
Our task required very good coordination of design works, prefabrication of steel elements, as well as logistics of deliveries and assembly itself due to the very short implementation time (less than 3 months).
Our task required very good coordination of design works, prefabrication of steel elements, as well as logistics of deliveries and assembly itself due to the very short implementation time (less than 3 months).
The properties of the supplied fuel turned out to be an additional challenge. During rainy periods, coal with a high content of clay minerals and subgrains stored on heaps becomes very sticky and dense. This causes rapid overgrowing of sections of narrowing chutes within:
- crushers,
- rotary feeders,
- chutes to the boiler.
- Design of the installation of pulse nozzles in five independently powered and controlled zones of the carburizing system.
- Matching the work of nozzles with other devices built into the carburizing system
- Redesign, prefabrication and assembly of some chutes (geometry correction) on sections most degraded by knocking.
- Installation of the compressed air supply system, pulse nozzles, control and power systems.
- Launching and optimizing control algorithms to ensure patency while reducing compressed air consumption.
- A multi-discipline project in the basic and as-built version.
- Pulse nozzle VA51C and VA60SS
- mounting elements of the MPS-TK-2 and MPN series
- Control cabinets based on Siemens LOGO programmable relays
What did we do as part of the project?
Based on the experience from previous implementations and an in-depth analysis of the fuel feeding process and the geometry of the carburizing system, we designed installations of pulse nozzles in five independently powered and controlled zones of the carburizing system. Our goal was to coordinate the operation of the nozzles with other devices built into the carburizing system for the best possible efficiency and a high level of automation. What is important, we couldn’t interfere with the master control system.
Redesigned chutes (after geometry correction), we made and built in the place of chutes degraded by knocking. The compressed air supply system was partially covered during the operation of the unit, which allowed for a significant reduction in the shutdown time of the unit for the installation of other devices. After installation and startup the installation of pulse nozzles was optimized (control algorithms) to ensure patency while reducing compressed air consumption. For the installation, we prepared a multi-discipline project in the basic and as-built version.