Dzięki systemowi dysz pulsacyjnych zagwarantowaliśmy stały przepływ materiału i usprawniliśmy produkcję.
Skutecznie wyeliminowaliśmy problem zalegania wełny mineralnej na ścianach filtra workowego. Dzięki zoptymalizowanej pracy dysz pulsacyjnych zapewniona jest ciągłość opróżniania filtra.
Czas realizacji
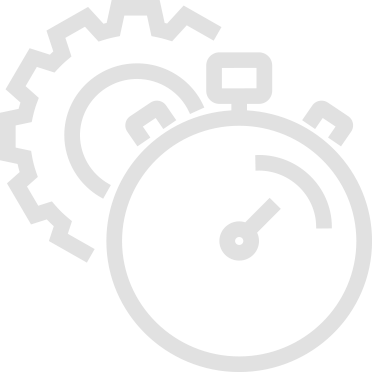
W czasie ruchu
Instalację doprowadzającą sprężone powietrze wraz z kolektorem sprężonego powietrza zamontowaliśmy na ruchu, bez konieczności zatrzymywania pracy filtra.
Podczas odstawienia w czasie jednej zmiany zakładowej
Dysze pulsacyjne oraz instalację zasilania udało nam się zamontować w czasie planowego odstawienia filtra workowego.
8 godzin czyli jedna zmiana
W tym czasie zamontowaliśmy dysze pulsacyjne z systemem sterowania i uruchomiliśmy gotową instalację.
Problem klienta
Wełna kumulowała się wewnątrz filtra, ściśle przylegając do jego ścian, a podajnik ślimakowy nie był w stanie zebrać całości materiału. Duże ilości osadzającej się wełny powodowały nawisy, które można było usunąć tylko manualnie, wchodząc do środka. Każda tego typu sytuacja wymagała odstawienia filtra i stwarzała poważne niebezpieczeństwo dla zdrowia pracowników czyszczących podajnik ręcznie.
Wyzwania
Największym wyzwaniem podczas projektowania tej instalacji była niepewność, czy zastosowanie dysz z jednej strony filtra nie będzie powodowało nowych problemów po drugiej stronie. W związku z tym przygotowaliśmy kolektor sprężonego powietrza na ewentualną rozbudowę całej instalacji.
Dodatkowym wyzwaniem była sprawna koordynacja prac. Zależało nam na tym, by montaż dysz i uruchomienie całej instalacji mogło odbyć się podczas krótkiego odstawienia planowanego.
- Szczegółowe testy materiału w laboratorium Polstage.
- Symulacja przepływu materiału.
- Dopasowanie systemu do wyzwań zakładu: dysze pulsacyjne VA51C o dużej energii (ponad 70 litrów powietrza w 0,25 sekundy).
- Montaż i uruchomienie systemu w zakładzie.
- Dysze pulsacyjne VA51C
- Elementy montażowe serii MPS
- Wzmocnienia miejsc montażu dysz przy pomocy dodatkowych blach
- Szafy sterownicze oparte o przekaźniki programowalne Siemens LOGO
Co zrobiliśmy w ramach projektu?
W procesie projektowania wykonaliśmy serię prób z materiałami na naszym stanowisku badawczym, co pozwoliło dokładniej określić parametry materiału oraz symulować ich uwalnianie za pomocą dysz pulsacyjnych.
Wykorzystując wcześniejsze doświadczenia oraz pozyskane dane i analizę geometrii filtra, zaprojektowaliśmy:
- ilość urządzeń,
- optymalne miejsca ich montażu,
- algorytmy sterowania.
W pierwszej kolejności podczas pracy filtra workowego zamontowaliśmy kolektor sprężonego powietrza, który wcześniej dostosowaliśmy do możliwości późniejszej rozbudowy instalacji. Następnie podczas odstawienia filtra wykonaliśmy dwa otwory w ścianach oraz zamontowaliśmy dysze wraz ze wzmacniającymi je blachami. Następnie uzbroiliśmy instalację w sprężone powietrze i uruchomiliśmy system. Całość prac została wykonana podczas trwania jednej zmiany zakładowej.