Bulk material no longer accumulates on the walls of the pipeline, even at the critical point of changing the angle of discharge. One pulse nozzle was enough to guarantee a constant flow and safe operation of the production line.
Lead time
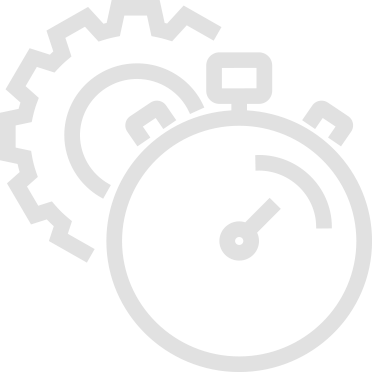
2 days
That’s the time it took to install the pulse nozzles on the chute to the Eirich mixer, made as one of the three installations installed in the plant. We equipped three places with pulse nozzles with collectors and controls.
8 hours or one shift
That’s how long it took us to assemble a single installation, including commissioning, testing the correctness of the system’s operation and training employees in the area of using the system. One change is enough.
Client problem
Bulk material (potassium sulfate) hangs on the walls of the pipeline. The most problematic is the place of changing the angle of repose.
Challenges
Insertion of the nozzle mounting element turned out to be quite a hassle. The transfer is made of a stainless steel pipe with a diameter of 300mm. Therefore, we designed an additional transition element, so we were able to safely and effectively mount the pulse nozzle. The designed part in the cylindrical element allows the installation of the nozzle, and also creates a flattened surface, which additionally improves the operation of the nozzle.
- Installation of one VA-51SS pulse nozzle.
- Programming of 3 nozzle operation algorithms that control the interruption of the device’s operation.
- Installation of one VA-51SS pulse nozzle.
- Mounting elements of the MPN series
- Control cabinets based on Siemens LOGO programmable relays
What did we do as a part of the project?
To allow the installation of a pulse nozzle supply manifold was prefabricated. In addition, we redesigned the mounting plate, so we were able to mount the MPN element on the pipe and prepare a control cabinet with three work algorithms.