Celem projektu była poprawa przepływu i zsypywania się dolomitu w betonowych zbiornikach magazynowych, w których występowały problemy z utrzymaniem ciągłości transportu materiału. W ramach realizacji zainstalowano system dysz pulsacyjnych zasilanych sprężonym powietrzem – w konfiguracji obejmującej 3 dysze pulsacyjne oraz kolektor powietrzny.
Harmonogram działań
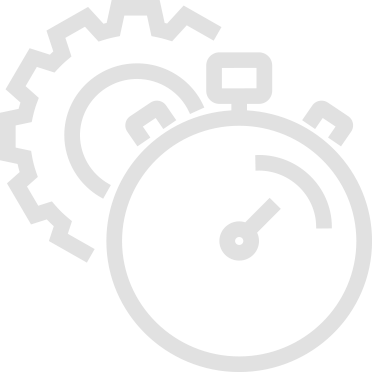
Etap przygotowawczy (przed montażem)
W pierwszej fazie projektu przeprowadzono:
-
analizę pracy zbiorników i właściwości przesypywanego dolomitu,
-
dobór odpowiedniego typu i rozmieszczenia dysz,
-
projekt układu pneumatycznego (kolektor + zasilanie powietrzem),
-
uzgodnienia z klientem dotyczące punktów montażowych, przebiegu rurociągów i integracji z istniejącym układem sprężonego powietrza,
-
przygotowanie zakresu prac do wykonania w czasie zaplanowanego przestoju instalacji.
Etap montażu i uruchomienia
Druga faza obejmowała fizyczny montaż instalacji i testy działania:
-
odwierty w grubych ścianach betonowych zbiorników – wymagające zastosowania specjalistycznych technik wiercenia i zabezpieczenia punktów montażowych przed pęknięciami,
-
montaż 3 dysz pulsacyjnych w zaplanowanych punktach zbiornika,
-
instalacja kolektora sprężonego powietrza oraz zasilania każdej dyszy,
-
sprawdzenie szczelności i wydajności układu,
-
uruchomienie i testy pracy układu pod obciążeniem,
-
regulacja parametrów pulsacji (czas, częstotliwość),
-
szkolenie personelu i przekazanie dokumentacji.
Problem klienta
Przed wdrożeniem systemu klient borykał się z typowymi problemami dla materiałów sypkich o nierównomiernej granulacji, jak dolomit:
-
zaleganie materiału przy ściankach zbiorników,
-
mostkowanie i blokowanie się dolomitu nad wylotem,
-
nieregularny zsyp materiału i tworzenie pustych przestrzeni (tuneli),
-
konieczność ręcznej interwencji, prowadzącej do przestojów i ryzyka dla obsługi.
Problemy te wpływały negatywnie na ciągłość procesu technologicznego i generowały koszty operacyjne związane z przestojami oraz konserwacją.
Wyzwania
Projekt wymagał zmierzenia się z kilkoma istotnymi wyzwaniami:
-
wiercenie w grubych betonowych ścianach zbiorników, co wymagało użycia narzędzi diamentowych oraz zachowania precyzji i bezpieczeństwa konstrukcji,
-
ograniczona dostępność przestrzeni wokół zbiorników i praca na wysokości,
-
zapewnienie zgodności z istniejącą infrastrukturą sprężonego powietrza,
-
zachowanie ciągłości pracy zakładu – montaż musiał odbyć się w wyznaczonym oknie postoju.
-
Zastosowaliśmy dysze pulsacyjne typu wysokociśnieniowego, odporne na zapylenie i przystosowane do pracy z materiałami mineralnymi.
-
Zaprojektowany i wykonany został kolektor powietrzny dopasowany do rozkładu zbiornika.
-
Dysze rozmieszczono tak, aby zapewnić efektywne czyszczenie stożka zsypowego i ograniczyć tworzenie zatorów.
-
System nie wymaga stałego nadzoru – pracuje automatycznie lub na sygnał operatora, co zwiększa bezpieczeństwo i ogranicza potrzebę ręcznej interwencji.
- Dysze pulsacyjne VA51-C
- Specjalne, skręcane elementy montażowe
Co zrobiliśmy w ramach projektu?
-
Analiza problemów eksploatacyjnych i warunków technicznych
Na początku przeprowadziliśmy wizję lokalną i analizę eksploatacji zbiorników, identyfikując miejsca powstawania zatorów, mostków materiałowych i problemów zsypowych. Ustalono przyczynę zalegania dolomitu oraz kluczowe punkty interwencji. -
Projekt rozwiązania technicznego
Na podstawie zebranych danych zaprojektowaliśmy system dysz pulsacyjnych, uwzględniając geometrię zbiornika, właściwości dolomitu i istniejącą infrastrukturę sprężonego powietrza. Dobrano odpowiedni typ dysz oraz zaplanowano ich rozmieszczenie, by zapewnić maksymalną skuteczność czyszczenia stożka zsypowego. -
Dostawa wszystkich komponentów systemu
Zamówiliśmy i dostarczyliśmy na miejsce wszystkie niezbędne elementy:
– 3 dysze pulsacyjne odporne na zapylenie i ścieranie,
– kolektor sprężonego powietrza dostosowany do warunków przemysłowych,
– rurociągi, zawory, elementy mocujące, złącza i osprzęt instalacyjny. -
Odwierty i montaż dysz w betonowych ścianach zbiornika
Przeprowadziliśmy specjalistyczne odwierty w grubych ścianach betonowych zbiorników przy użyciu technik diamentowych. Zapewniliśmy odpowiednie uszczelnienie i zabezpieczenie punktów montażowych, a następnie zamontowaliśmy dysze w zaplanowanych miejscach. -
Instalacja pneumatyczna i kolektor powietrza
Wykonaliśmy trasowanie i montaż rurociągów sprężonego powietrza oraz instalację kolektora z odpowiednimi przyłączami do każdej dyszy. Instalację podłączono do istniejącego systemu sprężonego powietrza w zakładzie. -
Uruchomienie i konfiguracja systemu
Po zakończeniu montażu przeprowadziliśmy próby szczelności oraz testy funkcjonalne systemu. Skonfigurowano parametry pracy dysz (czas trwania impulsu, częstotliwość), dostosowując je do charakterystyki dolomitu i rytmu pracy linii technologicznej. -
Przeszkolenie personelu obsługi
Zespół utrzymania ruchu został przeszkolony z zakresu:
– zasad działania systemu,
– obsługi eksploatacyjnej,
– harmonogramu przeglądów i serwisowania. -
Dokumentacja powykonawcza i przekazanie instalacji
Na zakończenie projektu klient otrzymał pełną dokumentację techniczną, schematy instalacji, instrukcje obsługi oraz zalecenia eksploatacyjne. System został przekazany do użytkowania.