Dzięki systemowi dysz pulsacyjnych zagwarantowaliśmy stały przepływ materiału i usprawniliśmy produkcję.
Pył drzewny z pozostałościami kleju nie okleja już ścian wysypu. Regularnie zsypuje się z filtra workowego do podajników.
Pierwszą instalację dysz pulsacyjnych zrealizowaliśmy jako projekt testowy, co pozwoliło dokładnie sprawdzić skuteczność naszego rozwiązania.
Czas realizacji
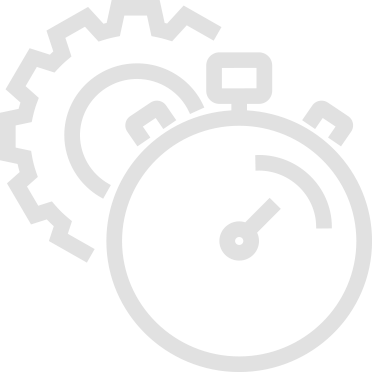
Przed realizacją
Nasz klient we własnym zakresie wykonał zabudowę kolektora sprężonego powietrza, a zrobił to w oparciu o nasz wcześniejszy projekt. Co ważne, zadanie udało się zrealizować podczas pracy systemu, bez konieczności zatrzymywania technologii.
Kilka dni od zlecenia
Tyle czasu zajęło nam przygotowanie uzgodnień technicznych, wytycznych montażowych oraz szczegółowego projektu rozmieszczenia dysz pulsacyjnych.
8 godzin czyli jedna zmiana
W tym czasie zamontowaliśmy dysze pulsacyjne z systemem sterowania i uruchomiliśmy gotową instalację.
Problem klienta
Pył drzewny wraz z pozostałościami kleju regularnie oblepiał ściany zsypu. Problemy z przemieszczaniem materiału do podajnika zmuszały kierownika utrzymania ruchu do częstego odstawiania technologii, a pracowników serwisowych do niebezpiecznego, ręcznego czyszczenia zbiornika. Coraz częściej pojawiały się też odstawienia awaryjne, które zaburzały pracę produkcji i generowały znaczne koszty.
Wyzwania
Pierwszym wyzwaniem był materiał w zsypach czyli pył drzewny z pozostałościami kleju. Powodował bardzo szybkie „zarastanie wysypu”, blokował zbiornik, a także tworzył mosty. Przez brak drożności konieczne było przerwanie produkcji i czyszczenie zbiornika.
Drugim wyzwaniem okazało się dopasowanie optymalnego rozmiaru dysz pulsacyjnych, sposobu ich rozmieszczenia oraz sterowania. Zależało nam na stworzeniu rozwiązania, które zagwarantuje drożność zsypu (przez uniemożliwienie przyklejania się materiału do ścian) przy jednoczesnym ograniczeniu możliwości podnoszenia materiału.
- Szczegółowe testy materiału w laboratorium Polstage.
- Symulacja przepływu materiału (pyłu drzewnego z resztkami kleju).
- Dopasowanie systemu do wyzwań zakładu: dysze pulsacyjne VA51C o dużej energii (ponad 70 litrów powietrza w 0,25 sekundy).
- Montaż i uruchomienie systemu w zakładzie.
- Wsparcie projektowe oraz wdrożenia systemów w pozostałych zakładach klienta na terenie Polski i Europy.
- Dysze pulsacyjne VA-51SS
- Elementy montażowe serii MPN
- Szafy sterownicze oparte o przekaźniki programowalne Siemens LOGO
Co zrobiliśmy w ramach projektu?
Na etapie projektowania instalacji, przeprowadziliśmy zaawansowaną symulację przepływu materiału oraz szczegółowe testy w laboratorium Polstage. Prace testowe pomogły nam dokładniej zbadać problem i precyzyjnie zaprojektować najlepsze rozwiązanie. Dzięki temu dopasowaliśmy optymalne rozmieszczenie urządzeń oraz algorytm sterowania.
Po okresie testowym klient doposażył w swoim zakładzie wszystkie filtry workowe w rozbudowaną instalację dysz pulsacyjnych (po dwie dysze VA-51C na sekcję).
W drugim etapie współpracy wdrożyliśmy instalację opartą o 2 dysze pulsacyjne VA-51C o dużej energii (urządzenia wyrzucają ponad 70 litrów powietrza w 0,25 sekundy). Takie rozwiązanie pozwoliło nam zminimalizować ilość dysz i tym samym ograniczyć ingerencję w poszycie filtra.
Finalnie udało nam się wyeliminować problem oblepiania ścian pyłem z resztkami kleju. System dysz zagwarantował stały zsyp materiału do podajnika.
Wraz z dyszami i armaturą dostarczyliśmy naszemu klientowi instalację zasilania oraz sterowania dyszami, a także wytyczne projektowe dla instalacji doprowadzającej sprężone powietrze.
W następnym kroku wspólnie zaprojektowaliśmy i wdrożyliśmy instalacje dysz pulsacyjnych w pozostałych zakładach naszego klienta. Teraz nieprzerwaną pracą cieszą się pracownicy działów utrzymania ruchu w Polsce i za granicą.